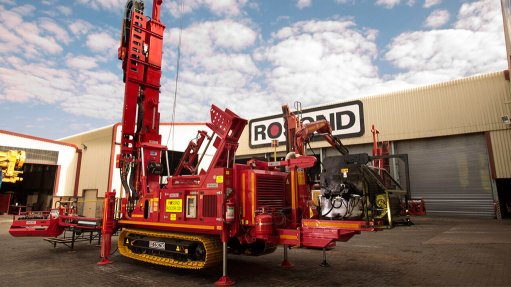
Two underground diamond drilling sites, both part of mining industry leader ROSOND (Pty) Ltd, have achieved impressive safety records of five years of “zero harm”.
Amandelbult Dishaba Underground Diamond Drilling, near Thabazimbi in the Limpopo province, achieved this milestone at the end of last year, while Evander Underground Diamond Drilling in Mpumalanga celebrated its accident-free record on 12 February.
Other ROSOND operations that have achieved notable safety successes in lost time injury (LTI) are the Rasimone South (5 years LTI on 5 December 2016), Kloof (5 years LTI on 19 December 2016), and the Amandelbult Tumela (5 years LTI on 28 February) sites.
Another three sites – Tau Tona, Amandelbult Dishaba, and Impala 4 – have experienced zero harm for 360 days.
Zero harm is defined as a situation where no injuries, not even minor ones, occur, while lost time injury (LTI) means that work time was lost due to an injury.
ROSOND, established over 50 years ago as RODIO/ROSOND, is active in underground mining development and exploration drilling, cementation works and pre-cementation of shafts as well as grout pack support systems.
Ricardo Ribeiro, Operations Director for ROSOND, says that underground diamond drilling has many hazards and the possibility for a serious accident is high.
“Activities require a great deal of manual handling and working conditions are physically demanding,” he says.
ROSOND has a policy of zero harm, and the safety of its employees is its first priority.
“We therefore scrutinise every possible hazard and do whatever is necessary to control and, if possible, eliminate the risks.”
Ribeiro attributes the drilling team’s success to several factors, including focusing on the top hazards and implementing various safety devices for the protection of employees.
The company has also gradually created a culture of safety through quarterly safety drives that remind employees of fundamentals and reinforce non-negotiables.
“Training programmes, including annual and refresher training, play a major role. Training concentrates on the safe operating procedures through theoretical and practical sessions facilitated by qualified trainers and assessors.”
Ribeiro adds that another driving force is objectives and targets.
“These are driven by a safety incentive scheme which rewards the teams with a safety bonus. Our partnership with our clients plays a big role through their safety programmes and standards.”
Supervisory staff also contribute by motivating drill teams.
Ribeiro concludes: “But it’s the drilling teams who are the heroes who make this possible. Without them, we do not have a business, and it is our responsibility to look after them and ensure they go home safely at the end of each day.
“We are extremely proud of this achievement and look forward to the next five years because we know that ‘zero harm’ is possible.”
ROSOND’s drilling includes development drilling, short hole (0-200m) and long hole (0-1000m) core drilling. Grouting comprises cover grouting, water and gas control and other specialised grouting works. ROSOND operates underground with several drilling machines and high-pressure cementation pumps and mixing equipment.
An important activity of ROSOND is the installation of grout packs – support systems that comprise the installation of automatic surface batching plants as well as underground relay stations. ROSOND operates several high pressure cementation pumps on surface and underground.