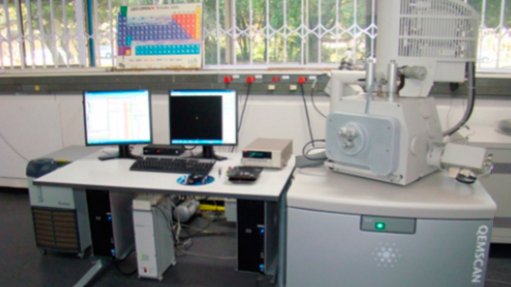
TECHNOLOGICAL INVESTMENT The Field emission gun Qemscan 650F implements chemistry and back-scatter electron signals to identify the mineral phases and determine their degree of liberation within particles
State-owned council for minerals technology Mintek has noted a 60% demand increase for its mineralogical services in the past five years, with a significant increase in analysis enquiries on graphites, manganese and phosphates, as well as a surge in inquiries from the platinum mining sector, Mintek Mineralogy manager Nosiphiwo Nyamane tells Mining Weekly.
“The bulk of these requests are mainly from junior mining companies that are more focused on exploration projects and investing more capital,” she says.
This demand for significant mineralogical analysis partially originates from depleting higher-grade ores, which necessitate a greater understanding of lower-grade ore mineralogy, prior to mining feasibility studies and processes, highlights Nyamane.
Owing to these and other capital for challenges, the mining industry requires a quick turnaround time on mineralogical analysis results, as this would reduce capital costs and provide perspective on the viability of continuing project exploration based on the most recent results, Nyamane says.
“As Mintek needs to keep abreast of the latest mineralogical technologies and methods to service clients by providing readily available analysis results, which assists in critical decision- making for mining projects, the mineralogy division invested significantly in the acquisition of several instruments and systems in the 2012/13 financial year,” she highlights.
These investments include a scanning electron microscope for quantitative evaluation of minerals, a fast chemical data collection system, which uses a combination of back-scattered scanning electron microscopy images and energy dispersive X-ray spectrometer analysis to create an image of a sample, based on chemical composition, and a Field emission gun mineral liberation analyser (Feg MLA) and Feg Qemscan.
The Feg MLA and Feg Qemscan both implement chemistry and back-scatter electron signals to identify the mineral phases and determine their degree of liberation within particles.
The Qemscan is a fast chemical data collection system, which uses a combination of back-scattered electron Scanning Electron Microscopy images and Energy Dispersive X-ray Spectrometer analysis to create an image of a sample based on chemical composition, explains Nyamane.
These images can then be processed offline to provide modal abundance, grain size, mode of occurrence and liberation information. Because the elemental proportions of each identified mineral are stored in the Qemscan’s database, a ‘chemical analysis’ can also be calculated, while new mineral information can be entered into the database as required.
The detailed analysis establishes not only the percentage of each mineral in the sample, but also the proportions of elements of interest contained in each mineral phase, whether it is in an easily accessible form, and how much is recoverable.
The information can be used to guide exploration, assess orebody delineation, develop processing routes and improve plant operations, she adds.
“Mineral texture and liberation potential are fundamental properties of ore and drive the ore’s economic treatment; therefore, the data gathered by the Feg MLA is invaluable to geologists and mineralogists,” Nyamane emphasises.
The mineralogy division also acquired an X-ray diffraction instrument, the Bruker D8 Advance XRD, which can analyse 90 samples at any time. It is used to identify the naturally occurring minerals or phases (synthetic mineral samples) present in a sample, based on their crystalline structural properties.
Nyamane notes that the division is also researching the benefits of using three-dimensional (3D) tomography for ore samples.
“Using a 3D X-ray computerised tomography scanner to examine the mineralogy of an ore sample can significantly improve analysis turnaround time, as little sample preparation is required,” Nyamane says.
While the division is conducting research using a 3D X-ray CT scanner at Stellenbosch University’s Central Analytical Facilities, in the Western Cape, it aims to offer this service to clients within the next three years – depending on the acquisition of such a multimillion-rand scanner.
Further, one of the latest offerings that the division has is geometallurgy, which involves the application of aspects of geology, such as applied mineralogy, in relation to extractive metallurgy and pyrometallurgy.