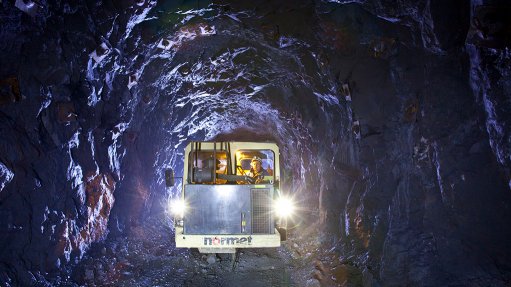
Name: Mayskoye mine.
Location: The mine is located in the Chaunski district of the Chukotka Autonomous region, in Russia.
Holding and Controlling Company: Polymetal International.
Brief Description: Mayskoye is one of Russia’s top high-grade refractory gold deposits, which was brought into the group’s production profile in 2011 as part of the Amursk hub project.
Mayskoye comprises an operating underground mine and an 850 000 t/d on-site flotation concentrator, launched in 2010 and 2013, respectively.
The operation primarily produces gold concentrate using the conventional flotation method, which is then shipped to third party offtakers or the Amursk pressure oxidation (POX) plant for further processing into gold doré bars.
Brief History: Mayskoye was first discovered in 1972 and was extensively explored between 1974 and 1986, mostly by surface diamond drilling. The deposit was the subject of several statutory feasibility studies conducted by the former Soviet Union and Russia.
Highland Gold acquired the licence for the deposit through a public auction in 2004. A feasibility study was completed by Aker Kvaerner and the development of the underground mine started in the first quarter of 2008. Substantial infrastructure was built on site, including road access and accommodation.
Polymetal acquired the mine from Highland Gold in 2009 and incorporated Mayskoye into the Amursk POX hub to reduce the construction of the processing plant.
Construction of the Mayskoye concentrator started in 2010 and mining operations started in 2011.
The mine was commissioned in 2012 and commercial production of gold concentrate started in April 2013. The deposit is expected to have a mine life of nine years.
The Mayskoye mine is expected to produce about 250 000 oz/y to 275 000 oz/y of gold.
Products: Gold.
Geology/Mineralisation: Gold mineralisation at Mayskoye is of the medium-sulphide, gold-pyrite-arsenopyrite type and is mostly associated with the steep quartz-feldspar dykes.
Economic gold mineralisation is confined to high-grade gold-quartz-sulphide veins. Only 46 of more than 300 veins were subjected to gold resource assessment, which were grouped into six mineralised zones to prioritise further mining operation scheduling.
The average orebody width is 0.8 m to 5.2 m and the zone of oxidation can be traced to a depth of 300 m. Gold in the oxidised zone can be found in free and sulphide-associated forms.
Reserves: Total proven and probable reserves as at January 1, 2018, were estimated at 6.65-million tonnes grading 6.6 g/t gold.
Resources: Total measured and indicated mineral resources as at January 1, 2018, were estimated at 1.92-million tonnes grading 11.7 g/t gold. Inferred resources were estimated at 9.45-million tonnes grading 10.3 g/t gold.
Mining Method: Underground and openpit.
Several underground mining methods are used at Mayskoye, but more than 80% of ore is mined by sub-level open stoping. Oxidised ore is mined in a series of shallow openpits, as well as the underground.
Major Infrastructure and Equipment: Primary ore from Mayskoye will be processed using conventional flotation at the 850 000 t/y circuit based on-site.
The circuit comprises single-stage crushing followed by three-stage grinding in one semiautogenous grinding mill and two ball mills and three-stage conventional flotation. The flotation concentrate is thickened, filtered, dried and packed into big bags, which are then transported to the Port of Pevek, for further transportation to the Amursk POX hub and third-party offtakers.
Conversely, oxidised ore is processed using conventional Resin-in-Leach (RIL) cyanidation. This process uses the same crushing and milling equipment as the flotation circuit, where slurry is subject to thickening, leaching, resin, resin deactivation, electrolysis and smelting. The cyanidation tailings are filtered and dry stacked in the lined tailings storage facility.
Owing to the refractory nature of Mayskoye ore, pretreatment oxidation processing is required, which is done at the Amursk POX hub that was launched in 2012. Autoclave leaching (POX) was selected as the most viable option.
Prospects: Owing to persistent problems with ore stability, which has been partly responsible for fatal accidents at the mine, Polymetal has accelerated a planned changeover from drift-and-fill mining to sublevel open stoping with backfill.
The new mining system has been designed to ensure that employees are not exposed to the falling rocks in the partially broken stopes since all development and production drilling will be done from waste openings. This new mining method has demonstrated positive dynamics, ensuring lower dilution from secondary stopes and reduced primary stope length.
Polymetal initiated a project to extract crown pillars at zones 1 and 2 using openpit mining in 2016. The openpit mine will deliver oxide and transitional ores, which will be processed through the retrofitted on-site processing plant that includes new cyanide leaching tanks and a tailings detoxification.
Contact: Polymetal investor relations Eugenia Onuschenko
Contact Details:
Polymetal International
Tel +44.20.7016.9506