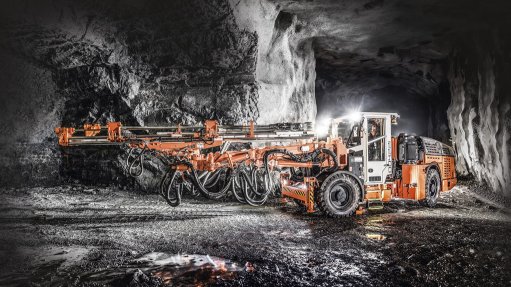
SANDVIK DD422i The drill rig, which includes bit-navigation and tele-remote tramming readiness, also employs software for blasting optimisation
Mining company Vedanta Resources’ Black Mountain base metals mine, in the Northern Cape, will later this year become the first local mine to adopt a new-generation jumbo drill rig equipped with an intelligent control system from high-technology engineering group Sandvik.
Sandvik underground drills business line manager Saltiel Pule says the automated Sandvik DD422i drill rig, to be used at Black Mountain for the tunnelling and blasting of a new decline shaft, is available with the company’s platinum automation level that allows full automatic face drilling functions.
The new drill rig provides a comprehensive list of visualisation display data, including hole position, angles and rollover information, drilled metres, the average penetration rate, the gross penetration rate and the various time counters, such as boom movements, drilling in full power, collaring and idling.
The drill rig, which includes bit navigation and tele-remote tramming readiness, also employs software for blasting optimisation.
“This drill rig started as a prototype in 2013 and [its development] was managed by Sandvik underground drilling product line manager Alain Comorge. The key objective was to offer customers a solution to global mining challenges such as increasing mining costs, safety, as well as rare drilling skills,” Pule explains.
Heis confident that the Sandvik DD422i has the widest range of automatic drilling functions available on the market, allowing for a significant reduction in cost and improved productivity.
“These advantages complement global trends, such as ecofriendliness, digitalisation, modularisation and automation, owing to mining houses and contractors looking for more cost-effective and efficient ways to mine.”
He adds that the percentage of overbreak and underbreak when drilling, as well as the ineffective measurement and control of tools, can increase mining costs. For example, when you overbreak, additional support and ventilation are needed, more tons need to be cleaned and there is ore dilution.
“By using the automation ability and the latest high-frequency drifters, the blast cycle times are reduced with improved penetration rates. The reduction of time wastage and improved productivity play an important role in any project optimisation,” Pule notes.
This is a consideration, as the cost of labour, he explains, especially for drill masters, is very high, owing to the difficulty and nonflexibility in their deployment as a result of the very high level of their skill.
While a shortage of skills may be prevalent in South Africa, Pule enthuses that the use of Sandvik’s AutoMine automation technology platform, in conjunction with the DD422i, means that the customers have the expertise available to negate this challenge, ensuring that technologically advanced mines remain in a position to achieve their production targets.
AutoMine provides a common platform from which automated processes – such as loading, hauling and drilling – can be controlled, he explains, adding that the platform has been used successfully since 2005 at mining company Petra Diamonds’ Finsch diamond mine, in the Northern Cape.
According to Pule, however, despite the integration of AutoMine, many performance characteristics – such as reporting, data collection, planning and designing – of the Sandvik DD422i drill rig are made possible as a result of its integration of iSure software for improved drilling and blasting parameters.
This software, he explains, allows for “absolute” precision in drilling, charging and blasting, enabling better ‘pull-out’. It also assists in achieving the critical requirement for optimum end-of-hole drill patterns.
“Mines are able to make use of skilled staff from Sandvik to assist in the operation of the DD422i, as it requires in-depth training,” Pule explains, adding that Sandvik provides support for the unit from its global and local resources in the initial execution phase and hands over the drill rig to the mine at the appropriate time, which could take three to six months, depending on learning curves.
Sandvik invests in the career paths of its local technicians and operational facilitators through the local Sandvik Training Academy, as well as a Sandvik Training Academy, in Finland, to ensure that operator instructors develop into drill masters over time.
Training at the centres takes weeks to complete and “requires individuals to attain certain milestones to be recognised as competent to effectively undertake a job at a customer’s site.”
Pule adds that the same training programme will be rolled out to upskill customers’ operational teams.
“Who knows – in the future, we may be exporting our drill rig supervisors globally to facilitate training,” he enthuses, noting that the idea is still new, but not impossible to develop.