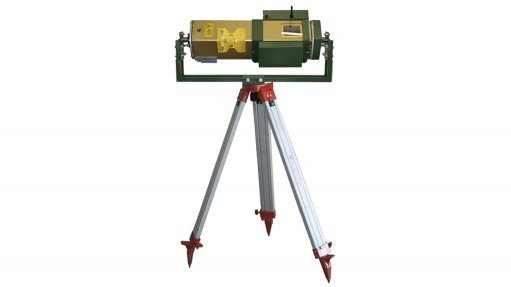
PREDICTIVE MILL MANAGEMENT MultoScan enables grinding mill operators to implement predictive liner replacement scheduling
Mining solutions manufacturer Multotec is rolling out a liner profile condition-monitoring service to customers in Africa, which uses its in-house-designed, highly accurate laser scanner, MultoScan, to offer significant cost-savings by improving the grind efficiency of mills.
Multotec MD Spike Taylor explains that, while each mill liner profile is designed to provide the correct trajectory to achieve either impact grinding or attrition grinding, depending on the application, the liners inevitably wear over time and affect the grind efficiency of the mill.
He notes that MultoScan has been tested in several applications and was deemed fit for market in May; however, it will not be made available for sale. Instead, the device will remain the property of Multotec, which offers condition monitoring free of charge using the device as a value-added service for customers using its linings.
Multotec’s condition monitoring unit uses MultoScan and Taylor states that the product has been “very well received” by South African customers, with interest in the service also growing from mines in West and Central Africa. MultoScan can be applied in a range of mining sectors, including base metals, platinum, diamonds and gold.
Taylor says offering MultoScan as part of a cohesive service rather than as a product on its own is proving highly beneficial, as the impetus is not on mines to provide any capital outlay to use the system. “It provides customers with information about the condition and efficiency of liners, which is highly beneficial to them in terms of improving their operations. They are very excited about this product as it gives them representative and reliable results.”
Taylor stresses that the MultoScan is substantially more cost effective than the alternative three-dimensional (3D) scanner available on the market, adding that MultoScan is also better suited to rubber mill liners, while the 3D scanner is more appropriate for steel mill liners.
He points out that it is standard practice for a liner supplier to conduct regular inspections of a client’s liner profiles to collect historical data to facilitate liner life predictions. This data, together with critical mill operating parameters, is used to estimate the point where a liner becomes inefficient and, thus, when a mill becomes inefficient. With this information, plant operators can decide when it is best to change liners to improve mill efficiency.
“The standard system for measuring liner profiles – the pin gauge method – is primitive, to say the least, time-consuming and often inaccurate. It involves inserting nails into the rubber plates and a pin profile gauge to get the profile of the lifter and measuring the length of the pin by hand to gather data. More importantly, measurement of this kind can be performed only when the mill shuts down, which is costly,” Taylor avers.
Identifying a need for a more sophisticated system, Multotec began work on an in-house laser-scanning design in 2013. MultoScan is a square tube with a single laser light that is mounted on a tripod with a levelling device. Taylor explains that, when the laser comes into contact with a component in the mill, the light is reflected into a camera and, depending on the angle of the reflection, the dimensions of the liner are automatically calculated and the degree of wear can be determined. MultoScan is also equipped with a WiFi device, enabling it to transmit data regarding the profiles of the lifters and shell plates to a receiving tablet.
Once the data is received, the company uses a data management system to analyse it and generate predictive replacement scheduling for a customer. “Graphs provide a visual display of how the liners are wearing over time and our customers can make decisions that will enhance the grind efficiency of their mills. The technology is simple, cost-effective, quick and reduces the time spent in the mill by personnel who would otherwise have to produce the measurements manually. It, moreover, yields consistent and accurate measurements.”
The system also provides an automatic measurement of the ball charge level, which is used to determine the ball trajectory of the worn liners. Significantly, there is no time lag on the information analysis. Once mill-performance data is collected and analysed, Multotec can discuss the change out of worn liners with clients.
Having access to accurate information on the liner profile, Taylor says, will also enable maintenance crews to exercise substantially more control over their liner inventories, subsequently enabling plants to reduce their liner stockholding.