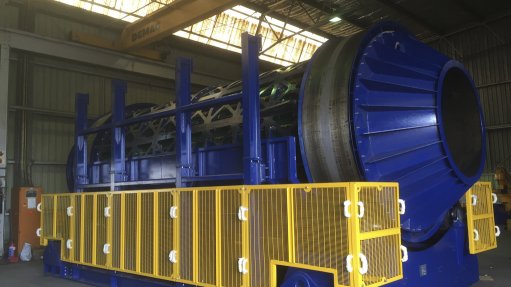
DOUBLE DUTY The trommels are used in pairs and are designed to accommodate double their usual load without failing
Pretoria-based vibration specialist Vipro Vibrating Products has delivered four large rotating drum screens, or trommels, to a diamond mining project in Gauteng, with commissioning scheduled to start next month.
These are the largest trommels supplied by the company to date, with the largest trommel weighing 30 t, including several unique design specifications, Vipro international sales and marketing manager Ryan Walker tells Mining Weekly.
With the development of more advanced technology and the high price of diamonds, he explains that the mine is reprocessing its historic dumps, screening anything larger than 1 mm in size. The trommels are designed to facilitate this screening by dewatering 221 t/h of kimberlite slurry at a volumetric flow of 995 m3/h.
The trommels were designed using engineering software that ensured that they were as light but also as strong as possible. Walker explains that the software enabled Vipro to identify stress areas that required reinforcement and, conversely, areas that were not under stress, which subsequently allowed for the use of lighter materials. The software also made it possible for the company to calculate how many cycles the trommels could withstand before fatiguing, as the mine requires the equipment to have an extended life expectancy.
The trommels, which are used in pairs, are designed to accommodate double their usual load without failing, should the mine decide to operate one pair for a period.
Vipro also opted to fabricate the outer drum from a laser-cut and rolled plate, rather than the welded and bolted lattice design used by many of its competitors. This, Walker explains, allowed for speedy assembly, and reduced tolerance creep. It also required less welding, which eliminated the need for the drum to be heat-treated. This method allowed for a lower profile of the outer drum, making the exterior of the drum smaller and lighter than most other designs.
The company also decided to use saddle tops instead of conventional angle-type stringers, which further enhanced the wear protection of the trommels’ components.
The drive system for the trommels consists of a centre drive geared unit, which powers the drive wheels through two cardan shafts. There are numerous integrated safety systems that allow the trommel to disengage or trip the power in the unlikely event that the drum moves out of its operating position.
Walker notes that, as Vipro has managed to build a sustainable client base over the past 20 years, rather than relying solely on project work, the company has been able to comfortably weather the current economic downturn in the mining industry. It is engaged in extensive research and development and aims to expand its product offering next year with a range of new designs.
“In these difficult economic times, mines are looking for solutions to manage their costs while enhancing operations. There is not a lot of project work available and, instead, companies are looking for solutions to the problems that are specific to their operations.
“Vipro aims to assist with this by manufacturing high-quality, maintenance-friendly equipment that offers the lowest possible cost of ownership and reliable, readily available components,” concludes Walker.