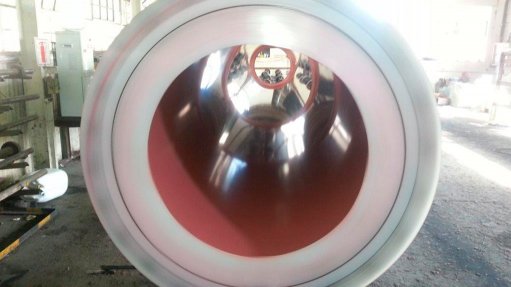
PRODUCT INNOVATION Nordbak has developed a new ceramic pipelining to ensure the cost effectiveness of pipelines at iron-ore mines
South African wear and corrosion solutions provider Nordbak says there has been a significant increase in demand for its lagged pulleys and ceramic pipe linings from South African iron-ore mines over the past two years.
“The significant increase in demand for the ceramic lining of pipelines can be attributed to Nordbak’s product quality assurance and the extended design life of its products,” says Nordbak business development manager Stefan Duvenage, adding that these features reduce downtime, extend the life of the customer’s capital and increase cost effectiveness.
Nordbak specialises in the manufacture of anticorrosion and wear- and abrasive-resistant coatings and compounds used in the linings of pipes, pipe bends, cyclones, pumps, valve launders, chutes, silos and tanks.
The company provides ongoing contractual services for several South African iron-ore mines, including the supply of crusher backing, pulley lagging and tailing pipe lining for Kumba Iron Ore’s Sishen mine and ferrous metals miner Assmang’s Beeshoek iron-ore mine.
It also provides pipe lining for Assmang’s Khumani mine and crusher backing for the Thabazimbi iron-ore mine, as well as services for steel producer Evraz Highveld Steel & Vanadium’s Mapochs mine.
The company’s African footprint extends to Sierra Leone, where it supplies crusher backing and lagged pulleys to mining companies African Minerals’ Tonkolili iron-ore mine and London Mining’s Marampa iron-ore mine.
Duvenage tells Mining Weekly that Nordbak’s wearing compounds have outlasted rubber linings by up to 12 times and, in some instances, such as in wear and abrasion applications, as much as 25 times.
With an industry presence of more than 50 years, Nordbak prioritises its commitment to continuous innovation, says Duvenage, noting that, in the last 18 months, the company developed a new ceramic pipelining to increase and ensure cost effectiveness.
The company’s engineering division also manufactures and lags pulleys for the mining industry to SANS 1669-1:2008 and SANS 1669-2:2008 specifications. Pulleys lagged by Nordbak at its Wadeville factory also carry a one-year guarantee, which is unheard of in this industry, Duvenage says, noting that it is also accompanied by a SANS 1669 certificate.
“The Nordbak high-impact pulley compound has been extensively tested against the SANS 1669:2008 standard and complies with and exceeds the standard in all aspects,” he says, highlighting that the pulley compound indicated an extended product life – up to ten times more than the life of rubber linings – during trial periods at major mining houses.
Further, Duvenage cites adhesion as a key factor that contributes to a product’s success in terms of quality and life, noting that Nordbak’s wearing compounds have a natural adhesion to steel and concrete, forming an integral bond with the surface and do not allow for ingress of foreign matter between the bonded surfaces, which, in turn, reduces corrosion.
He adds that pulleys, lagged with the Nordbak pulley compound, have been run- ning for more than ten years at an iron-ore mine in the Northern Cape, resulting in reduced downtime and providing significant capital savings for the mine.