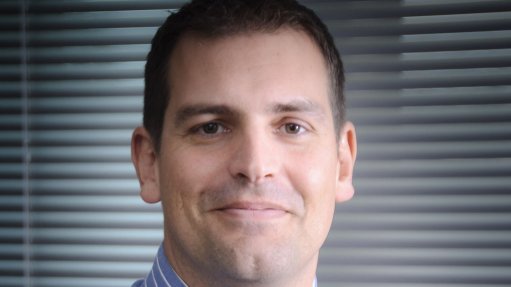
RUI GOMES Being able to develop and implement changes to produce greater efficiency is important in the pumps industry
Specialist slurry equipment solutions provider Weir Minerals is introducing the next-generation Warman horizontal froth pump, which features a continuous air removal system that can be applied to the company’s froth pumps already in the market.
This is in line with Weir Minerals’ focus on continuously developing its flagship Warman range of slurry pumps to enhance and improve its products to meet the needs of clients across the company’s global footprint.
Weir Minerals Africa slurry pumps pro- duct manager Rui Gomes says creating froth in mineral processing plants is an integral part of extracting copper and other base metals. He explains that, through the introduction of chemicals for effective separa- tion, the recovered material is transported to the next process stage in this form, pre- senting a challenge from a pumping perspective.
“The company has looked at different solutions for the effective pumping of froth, especially as it is difficult to transport tenacious froth using a centrifugal pump once air bubbles have formed.”
He highlights that, in the past, the methods used by the company included integrated tank- type vertical pumps. The open top tank allows for the bubbles to be liberated into the atmosphere and this enables the product to flow into the pump. However, one of the major limitations of this method was efficiency, as the tank size limited the amount of product that could be moved.
Gomes says another method the company employed in the past was oversizing a stan- dard horizontal centrifugal pump. The major downfall with this was that the pump would be significantly oversized to increase the inlet size and, in all cases, more power was needed to accommodate the larger pump size.
New Methodology
Weir Minerals’ new froth pump design aims to remove froth more efficiently. The Continuous Air Removal System (CARS) is designed to separate and remove gas in tenacious froth applications, resulting in more efficient pumping.
Gomes notes that the company has increased the inlet size of the pump to allow for a much larger amount of product to flow into the pump and reduce the inlet velocities into the pump.
He explains that the first stage of the pump system is the patented Warman froth-inducer blade impeller. This promotes movement of the froth slurry into the eye of the impeller, while simultaneously prerotating the product and initiating the separation of the high gas content in the froth towards the centre of the inlet and the vent holes located on the impeller back shroud.
The design also has a secondary inducer mounted on the shaft, behind the impeller at the back of the pump. As a result, the high gas content moves towards the back of the pump, allowing air to escape into the atmosphere through a venting chamber, with the liquid remaining in the impeller.
“The inducer impeller and oversized inlet allow for the froth or viscous slurries to be effectively moved into the impeller to be transported to the next destination.”
Features and Benefits
The open-type impeller is a “unique feature” of the pump and has inducer vanes that scoop the froth into the eye of the impeller, allowing for effective pumping, as there is no air locking at the impeller’s eye.
This method also allows for stable pumping performance with improved product retention, owing to sump overflow, and the CARS venting system can be routed back to the suction tank.
Gomes emphasises that, with the techno- logy and design of the impeller and the inducing vanes, air removal is still a key factor in terms of pumping froth, adding that the new method can, therefore, be easily implemented, as the transition involves installing a couple of additional parts on existing Warman AH or AHF pumps.
“Slight modifications are made to the Warman AHF pump. Our customers who own older Warman AHF froth pumps can upgrade their models by simply installing the components that allow air to be removed from the froth slurry, as it is a modification to the existing pump.”
As the system is locally manufactured, Weir Minerals Africa offers its clients a quick turnaround time on orders.
Gomes concludes that being able to develop and implement changes to produce greater efficiency is important in the pumps industry, as it allows for company growth in terms of having the necessary equipment available, as well as industry growth with regard to improving equipment and solutions, which, in turn, ensures better project efficiency.