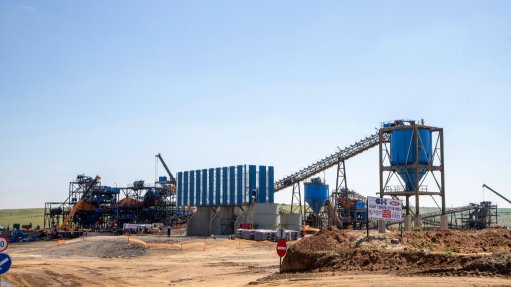
SUSTAINABLE TECHNOLOGY Upgrades to the Gugulethu plant are designed to promote the sustainable use of water
Coal exploration and mining company Canyon Coal reports that its newly commissioned 40 t/h filter press at its Mpumalanga-based Gugulethu mine is assisting in improving its sustainable use of water.
Canyon Coal developed the Gugulethu mine as a greenfield operation within 12 months and extracted its first coal within the first few weeks of this year, and it intends to continue development of the mine with the commissioning of a 400 t/h processing plant.
Canyon Coal COO Jarmi Steyn indicates that the installation of a filter press forms part of the Gugulethu plant upgrade, emphasising the need to have measures in place to advance effective water management practices.
“The filter press uses high-pressure dewatering technology to separate water from solid waste materials. Having a filter press is proven to be one of the best ways to process slurry efficiently and conserve water,” she explains.
Steyn adds that efficient slurry processing also leads to a reduction in contamination risks, noting that, once separated from solids- containing tailings water, filtered process water can be reused for beneficiation and dust suppression applications at the mine.
Prior to the issuing of a water-use licence for the mine, Canyon Coal undertook specialist studies on the surrounding wetlands and biodiversity, leading to the creation at the mine of a 200 m buffer zone to protect the surrounding Klein Olifants water course.
Steyn says that Canyon Coal has a competent environmental team that oversees the effects of its operations, also ensuring that the company complies with relevant environmental legislation.
She also tells Mining Weekly that the Gugulethu mine is continuing to expand production operations with the aim of reaching steady-state production before the end of this year.
In this regard, the processing plant has progressed through cold commissioning to ensure that all the components, such as gearboxes and pumps, are working properly. “This was followed by hot commissioning with coal and water,” Steyn highlights.
The company expects to produce an estimated 200 000 t of run-of-mine coal a month, to be processed for export markets.