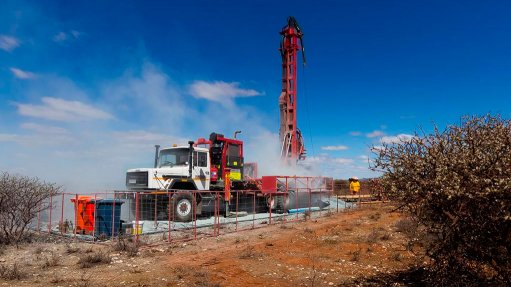
PERCUSSION DRILL RIG Rosond has 27 drill rigs at a brownfield exploration project near Kumba Iron Ore’s Kolomela mine, including a persussion drill rig
Photo by: Rosond
The exploration team at a brownfield project, near mining major Anglo American’s iron-ore business unit Kumba Iron Ore’s Kolomela mine, in the Northern Cape, reached 670 lost-time injury-free days (LTIF) at the start of last month, confirms drilling and grouting services provider Rosond.
“This is one of the largest exploration projects currently taking place in Africa. We are performing well and are achieving the production rates Kumba requires, but, most of all, we are doing this safely,” says Rosond exploration director Omer Mees.
The project, which is headed by Kumba’s geoscience division, has about 300 exploration personnel, half of whom are contracted Rosond employees.
Mees tells Mining Weekly that Rosond has been providing exploration drilling for the project since February 2012. “Kumba Iron Ore Exploration has high safety standards and Rosond is committed to ensuring compliance to these rules and regulations, which is often challenging. Nevertheless, the current safety record is testament to the dedication and collaboration of both parties in the realisation of zero harm.”
He adds, however, that drilling operations at iron-ore sites are always challenging, not only because of the mineral formation and the host rock – which is difficult to drill – but also because of the pace required by Kumba.
Rosond has 27 drill rigs on site, comprising the company’s standard Rocor diamond drill, a percussion drill and a new diamond drill that was introduced in August and which features a prototype, automated rod-handling system control.
Rosond designed the new drill in collaboration with Italy-based drill rig manufacturer Comacchio.
“We are testing the new rig’s performance to ascertain whether it can maintain the production levels of manual drill rigs, because automated drilling systems are generally a bit slower than manual systems.”
Mees points out that it is too early for Rosond to determine whether the drill rig is performing well or for the company to calibrate its performance. “We would have to run the machine for a few more months before we can do a decent comparison between the automated and manual drill rigs.”
Rosond established a training centre in the Northern Cape last year, which provides all new employees with induction training and a yearly refresher induction programme.
“We also have safety training and a refresher safety course that takes place every year. This training involves understanding all the safety procedures and standard operating procedures associated with working at a mine, including transport, materials handling and drill rig operating procedures,” explains Mees.
He adds that the training aspects specific to drilling include transporting the equipment, setting up a drill site and daily drilling practices, such as pulling and lowering drilling rods, as well as extracting core samples.