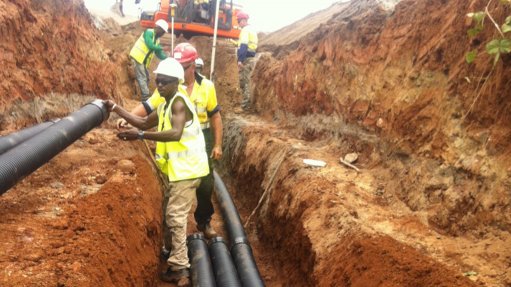
PIPING SOLUTION INSTALLATION Polypipe supplied its Ridgidrain high-density polyethylene piping solution to an iron-ore mine in Sierra Leone
UK-based pipe manufacturer Polypipe is ready to expand its presence in the African market and is homing in on the mining industry, having already secured contracts to supply pipework systems to major mining projects, in Kenya and Sierra Leone, in the last two years.
Speaking to Mining Weekly on the sidelines of this year’s Investing in African Mining Indaba, Polypipe export sales manager Philip Wood said the company in December supplied its Ridgidrain high-density polyethylene (HDPE) piping solution for use at an iron-ore mine, in Sierra Leone's Port Loko district.
“The Ridgidrain HDPE piping solution was supplied to manage water decanting from the tailings at the iron-ore mine into a pipeline that will drain the water in the tailings dam wall to a local water-treatment area,” explained Wood.
He added that HDPE was the material of choice in many mining applications, as it was ideally suited to rugged terrain, extreme climates and changing site environments.
“After a competitive tendering process, we won the order in January 2013 by demonstrating our ability to manufacture pipes in accordance with extremely tight supply deadlines and to pull products from Polypipe’s various manufacturing sites, in the UK, together into one consignment,” Wood enthused.
He described Polypipe’s Ridgidrain as a twinwall system that offered a complete solution for non-pressurised surface and subsurface drainage applications, as it was lightweight and offered high compression strength with an easy push-fit installation system.
Wood added that the Ridgidrain piping solution offered better time and cost savings than those of traditional systems. “It requires no heavy-lifting equipment on site, as it is about 94% lighter than traditional concrete systems, making it easier to handle. This, in turn, considerably reduces transportation and on-site plant hire costs.
“Further, Ridgidrain is usually manufactured in 6 m lengths, but the consignment was specified to be 5.8 m to allow for the internal dimensions of the shipping containers and to provide maximum on-board shipping capacity,” he pointed out.
Wood added that 10 mm x 150 mm Ridgidrain pipes and associated fittings were also shipped from the UK to Sierra Leone in August 2013.
“When you are delivering a key component for major infrastructure work, such as for this project, you have to be aware of how vital it is to work according to the customer’s shipping requirements and schedules. One of our strengths is manufacturing to tight deadlines, so we do not adhere to rigid production schedules. We believe in flexibility and will manufacture what the customers want, when they want it,” he concluded.