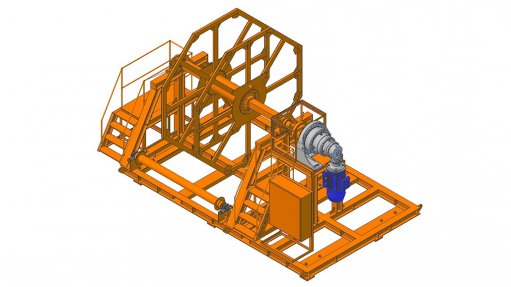
VERSATILE MACHINERY Belt reelers can handle narrow to wide belts and can be handled with one unit that is adjustable for various belt widths
Equipment manufacturer Dymot Engineering Company has developed an electronic belt tension control system (BTS) for mines that use high speed, large capacity and long length conveyors as an alternative to gravity take-up systems for the tensioning of high production machines.
Largely supplying base metal mines, or mines which offer base metals as a by-product to their main mining activities, Dymot says the system incorporates a variable frequency drive (VFD) to offer torque control to maintain belt tension, which is set through the machine’s human-machine interface (HMI) and the VFD to the required tension, such as for prestart and running tension.
The company supplies base metal mines in countries such as Zimbabwe, Zambia, Peru, Chile, Madagascar, Finland, Dubai, Panama and Kazakhstan.
“Manual operation for tensioning and slacking the belt for maintenance and/or emergencies comes standard with the system. The HMI displays the belt tension in both static and operational modes,” the company says.
Dymot Engineering Company adds that once the main belt is at speed, or per time factor (settable), the VFD maintains the running tension.
After ten seconds at the same tension level, the brake will park the winch and the system will only monitor the tension fluctuations and react accordingly.
When the main belt is stopped, the BTS will release tension through the VFD to the preset point.
The benefits of the BTS system include manual control possibilities, fault monitoring capabilities, over and under tension tripping, recording through the HMI and communication possibilities to the plant.
Dymot also supplies braked capstans, which it says work in conjunction with horizontal gravity take-up systems. The purpose of these in a conveyor tensioning rope system is to prevent shock loads – which are caused by a power failure or emergency stops – from pulling excessive rope from the system and causing the counterweight to hit the top of the gravity take-up tower.
This is achieved by wrapping the rope through a braked and grooved bull wheel system, the company explains.
Dymot Engineering Company adds that the hydraulically-released caliper disc brakes are held in a normally “off” position and fail to a “save” position in the event of power loss. This is controlled by a hydraulic power pack.
In the event of a conveyor power failure or emergency stop, the power supply to the power pack is lost and the caliper brakes engage. The subsequent momentary shock load arising from the conveyor will be absorbed by the capstan brake and will not pass through to the take-up tower, Dymot Engineering Company explains.
In addition, the company says it has also built “one of the biggest” braked capstans, to date, in the world, with a brake capacity of 60 t.
Another beneficial product Dymot Engineering Company supplies to many base metals mines are belt reelers, largely owing to modern mining methods having created a demand for handling longer and wider belts.
“With less splicing preferred, conveyor belts are shipped in longer lengths. The proper equipment is required to handle these belts,” the company says, referring to its development of heavy-duty conveyor belt reelers that can handle narrow to wide belts and can be handled with one unit that is adjustable for various belt widths.
“This is a great advantage for the mine as one unit can service most conveyors on site,” the company states.
Some of Dymot Engineering Company’s other developments include plant manoeuvring winches, rail car moving systems, hydraulic winches and rope sheaves, as well as barge moving winches, mill rotating winches, and stage and construction winches.
Dymot Engineering Company has been in operation since 1965, and supplies more than 54 countries globally.
Dymot is also ISO 9001:2015 certified.