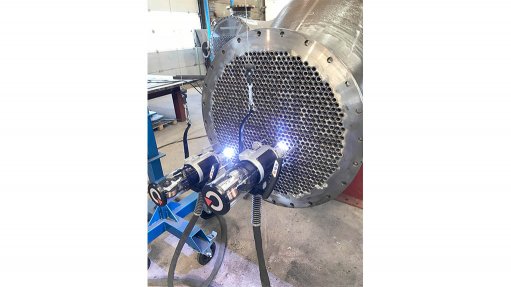
TAKING ORDERS To manage its increasing orders of heat exchangers while constantly raising its production standards, the company has invested in orbital tube-to-tubesheet technology from leading original-equipment manufacturer Polysoude
An even higher standard of welding on heat exchangers will now be achieved by specialist fabrication company Efficient Engineering, with the installation of two orbital welding machines from France.
In the construction of heat exchangers, the welding of the tube to tubesheet connections is known to be a challenging task, says Efficient Engineering quality manager and welding engineer Dries Vandezande.
To manage its increased heat exchanger orders while constantly raising its production standards, the company has invested in orbital tube-to-tubesheet technology from leading original-equipment manufacturer Polysoude.
“These machines will provide excellent repeatable results on every job, delivering consistency in the weld profile. These welds are very demanding, and require a level of welding skill which is in short supply in South Africa,” says Vandezande.
While a manual operator would have interruptions as he does both sides of the weld, which can produce defects such as pinholes, the orbital welding machine conducts the whole weld in one pass.
The quality result is ensured by a pre-programmed welding procedure, he explains. The procedure qualification record (PQR) will assure the customer that, as long as the base material and joint preparation is consistent, the same high level of results will be achieved.
“Predictability is important for our customers, and this orbital technology raises the bar on that score. It is especially important for many of the more exotic materials that you can provide that predictability that the weld is going to be sound,” he says.
The units can weld a range of material from stainless steel and carbon steel to low alloys – and with the application of different welding heads, exotic materials like titanium.
Among the key features of the orbital welding machine is its arc voltage control, he explains, which achieves a consistent weld bead. After pre-programming, the arc voltage control keeps the weld pool constant to deliver the welds predicted in the PQRs.
The advanced orbital welding machines can also be applied, with different accessories, to header boxes where limited access through holes only is available.
“This is very novel technology, which opens up a new world for Efficient Engineering. When there is market demand, we will be able to apply welding techniques that deliver the best results. This overcomes the challenges with manual welding that the risk of defects and the challenge to repair them are high,” he says.
The new orbital welding machines also bring safety benefits, he says, especially related to the pre-heating of the pieces to be welded. Certain alloy materials could require pre-heating up to 150 °C or even 250 °C. With the orbital welding machine, the operator is at a safer distance from the test piece.
Efficient Engineering is a member of industry body the Southern African Institute of Welding.