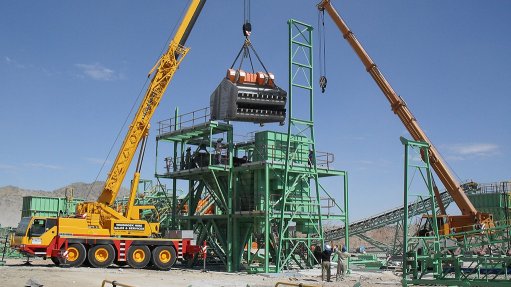
PREFERRED EQUIPMENT A Joest vibrating screen in a gold application in Namibia
Specialist vibrating equipment manufacturer and supplier Joest’s screens are customised to match the metallurgical requirements of a client’s processes and the associated mechanical duty, as part of the company’s ‘Engineered Solutions’ approach aimed at supplying clients with a total solution.
“Our customised screens are often the preferred equipment owing to their robust design and proven performance. Understanding the difference in design and duty for process plant screens, particularly sizing feed preparation in washing and dense-media separation (DMS) applications, is a key feature of our ongoing success in other sectors of the mineral processing industry,” says Joest CEO Derrick Alston.
The company says itcontinues to make inroads into Africa. “We have supplied six vibrating screens to a gold mine in Liberia, eight vibrating screens to a gold mine in Mali and 15 vibrating screens to a gold mine in Burkina Faso,” notes Joest general sales manager Yashin Ramdhin.
Joest has also supplied screens to an operation in Tanzania and has had vibratory feeders installed in a large coal mine in Mozambique. The company is optimistic that its business in Africa will go from strength to strength.
This belief stems from the favourable reputation that the Joest brand has gained over the years. A particular advantage of Joest’s equipment is its increased life span, structural integrity and ease of maintenance, which is particularly important in remote areas in Africa.
Joest offers a full selection of specialist equipment to meet its customers’ total vibrating screen and feeder requirements. Ramdhin says the company’s specialist vibrating equipment forms part of a tailored solutions approach to cater for a range of duties, “which allow our customers to reduce downtime and achieve production efficiencies at the lowest operating costs”.
An example of Joest’s ‘Engineered Solutions’ approach is its design and development of a 4.3-m-wide banana screen to cater for the ongoing trend in the coal-processing sector to opt for larger equipment so as to increase throughput and boost efficiencies.
“This has had an impact on the entire equipment supply chain, from screens through to cyclones and centrifuges. Joest has, therefore, been ideally positioned to incorporate the latest advances into its own 4.3-m-wide screen, which means that the coal processing sector in South Africa can now be confident it is on par with what is happening internationally,” says the company.
“We have paid close attention to our clients’ needs by assessing the failure modes of existing 4.3-m-wide screens from other suppliers in this market and designed our screen with the focus on reduced downtime and ease of maintenance when required,” notes Alston.
He adds that there are 50 to 60 screens of this size in the coal-processing sector at present, many of which are approaching the point in their life cycle where they will need to be replaced. Joest’s new 4.3-m-wide screen, which incorporates the latest technology and refinements, is therefore ideally positioned to fill this gap in the market.
Meanwhile, Joest’s screens are also making significant inroads into the iron-ore industry in Africa.
It has supplied and installed 20 screens at South African mining company Kumba Iron Ore’s Sishen mine, at Kathu, in the Northern Cape – the largest iron-ore mining operation in South Africa. The new Joest 2.4 m × 4.8 m single-deck exciter driven screens for Sishen replace ageing screens in the original plant installation, which have been operating for about 40 years.
These float-and-sink screens are located in the DMS plant where cast iron cyclones separate the iron-ore from the tailings. “The exciter driven screens provide an increased G-force which should result in improved recovery of ferrosilicon media as well as reduced maintenance costs,” Alston notes.
The order is the culmination of Joest’s 15-year-long relationship with Kumba Iron Ore. It is also a testament to the applicability of these customised designed screens for such rugged applications as the iron-ore and manganese sector in the Northern Cape in particular. Joest recently established a branch at Kathu, which is run by the newly appointed branch manager, with the main objective of carrying spare components for Joest’s equipment.