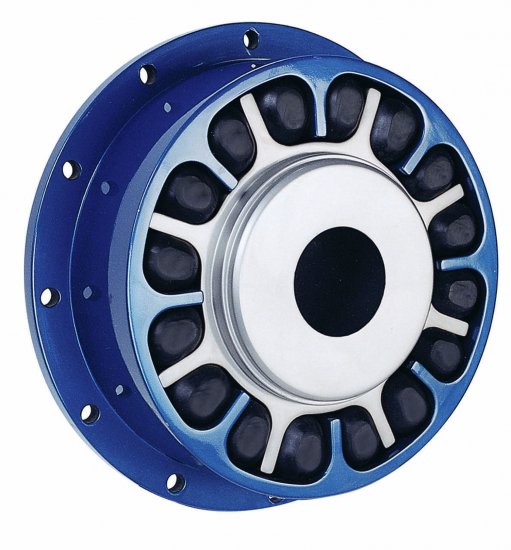
COUPLING SOLUTION The Info.Base guides share Renold's specialist engineering knowledge and expertise on couplings and gears
UK-based industrial power transmission manufacturer Renold last month published a free guide on the use of rubber-in-compression couplings for mining and quarrying applications, says Renold business development director Alan Dean.
This guide, titled Coupling Solutions: Rubber-in-Compression, marks the first of the newly launched series of Info.Base guides, and addresses issues such as backlash, extreme vibration, safety, reliability, how to decrease the need for maintenance and how to reduce lifetime operating costs in mines and quarries.
The coupling guide highlights certain applications in mines that can be improved in terms of on-site maintenance by fitting Renold Hi-Tec rubber-in-compression couplings.
Renold’s series of Info.Base publications is designed to assist engineers with many of the daily issues associated with power transmission systems installed at industrial plants and on equipment and machinery.
The guides share Renold’s specialist engineering knowledge and expertise on couplings and gears, as well as useful and practical ‘how to’ tips and informative application-based content.
Dean adds that the rubber-in-compression couplings guide explains the common causes of recurring problems such as torque amplification and motor hunting on inclined conveyors, and demonstrates how rubber-in-compression couplings can provide the solution.
Renold’s Product Offering
Rubber-in-compression couplings are comprised of two round metal sections that fit inside each other, with the two paddles projecting inwards from the outer section and outwards from the inner section.
Dean highlights that its Renold Hi-Tec rubber-in-compression coupling is maintenance-free and can reduce the levels of on-site noise and vibration, which extends plant life.
Further, as the Renold Hi-Tec rubber-in-compression coupling is fail-safe, it ensures that the drive is always maintained, resulting in a safer working environment, he says.
Rubber blocks are placed in the spaces between the paddles and, as the motor turns the outer section, it drives the inner section through the rubber blocks. While this happens, the rubber is compressed – hence, the term ‘rubber-in-compression’.
“When rubber is loaded ‘in compression’, it reacts as if it were an incompressible fluid and is inherently strong and robust. Rubber-in-compression couplings are intrinsically fail-safe because, even if the impossible happened and the rubber blocks were destroyed, the strong metal paddles would come together to provide the drive,” explains Dean.
“In 1996, Renold acquired the rubber- in-compression side of Holset Engineering, subsequently adding rubber-in-compression couplings to its range. Renold Hi-Tec couplings are used in many demanding applications, such as in the steel industry, mining and quarrying, mass transit, marine and power generation,” he says.
Importance of Maintenance
Renold highlights the importance of maintenance in mining in terms of cost and health and safety, adding that if mining equipment is poorly maintained, it can lead to failures, which result in downtime and a loss of revenue.
Plant and equipment failures can also result in injury or death. For example, if the drive coupling fails on a mine winder, it can cause the cage to drop, which could result in death or injury.
Dean adds that some plant equipment is difficult to access, as it is used in harsh environments, which can also lead to poor maintenance.
Mines can tackle this challenge by fitting maintenance-free products, or buying or renting products that do not require constant maintenance, he concludes.