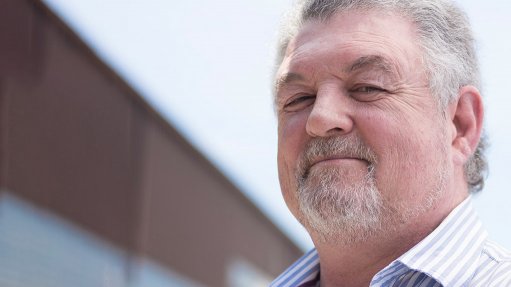
ANTHONY YELL We have supplied mill and scrubber trommel screens to the four corners of the earth
Preventive maintenance is key in ensuring the longevity of trommel screens, says mineral processing equipment and solutions provider Multotec.
The company adds that the high wear rates of the screen media, as a result of the high peripheral speed of the trommel screen itself, are a significant problem associated with larger trommel screens.
“Multotec is well positioned to develop screen media to face these challenges in either polyurethane, rubber, steel, ceramics or combinations of these. The company is continuously developing screen media to suit specific applications. No two applications are the same and, therefore, each wear solution is unique,” explains Multotec screening product manager Anthony Yell.
In addition, a trend towards larger mills is giving rise to higher flow rates and velocities, which, in turn, increase wear rates.
“Double the velocity on a polyurethane screen equates to an increase in the wear rate by a factor of five,” he notes, adding that the challenge is to develop screen media to give acceptable wear life.
Multotec are doing extensive research on different materials to improve wear life on an ongoing basis.
The company also has the added advantage of being able to supply polyurethane panels for smaller feed sizes where the main wear criteria are sliding abrasion and wear impact on rubber panels. “We design and manufacture rubber and polyurethane panels in-house,” Yell points out.
He explains that the company has had trommel screens running for over ten years that are still operational and that customers can return trommel screens for refurbishment as part of their preventive maintenance.
The rubber lining is stripped off the steel structure, visually inspected for wear and then nondestructive testing is carried out to determine the integrity of the trommel structure. “If it is still within specification, it can be shot-blasted and re-rubber-lined, whereupon it will be good to go for many more years,” he adds.
The time taken to refurbish the trommel screens is dependent on the work required. If, after the rubber lining is stripped off, the magnetic particle inspection testing is completed and the frame is in good condition, the unit will be relined with rubber and returned in about four weeks; however, if there is damage to the trommel steel structure, refurbishment could take up to ten weeks.
Refurbishing the unit once every two to three years can extend the life of the trommel to over ten years.
“We are presently in an economic downturn; however, there has been a steady increase in the demand for trommel screens and we expect the trend to continue owing to the growing number of mines worldwide,” recounts Yell.
Trommel screens have a certain niche in the market and are used in three main areas: sag and ball milling in copper, gold and platinum- group metals and in potash and phosphates for tramp removal.
Mill and scrubber trommels are also used in scrubber product sizing in diamond mining and in the removal of organic material in mineral sands; these trommels do not require their own drive system or foundation; therefore, if compared to vibrating screens in these applications, they are a very cost-effective solution.
Yell notes: “In mineral sands operations, they have proved to be more effective than vibrating screens in the removal of organic matter as they do not build up.”
Multotec has manufacturing plants in South Africa and Chile and can also supply spare parts from South Africa, Australia, Chile and the US, which reduces the supply chain dramatically and extends its geographic footprint.
“We have supplied mill and scrubber trommel screens to the four corners of the earth, from South America to Papua New Guinea and Siberia to Kazakhstan. There are not many places where they are not prevalent, as the Multotec product has proved to be highly reliable,” he concludes.