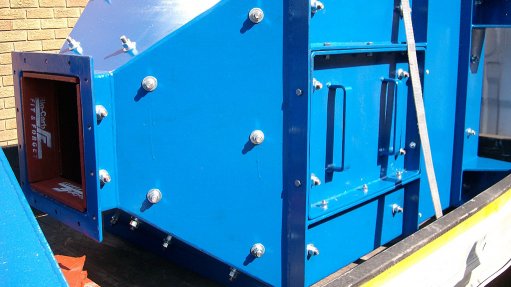
CHUTE REFURBISHMENT Rio-Carb is currently rolling out a 16-chute refurbishment programme at a coal mine in Vanderbijlpark
Liner plate expert Rio-Carb will install its chromium carbide (CrC) alloy long-life wear plates later this month in one of the chutes at a Vanderbijlpark-based coal mine, as part of a 16-chute refurbishment project.
Rio-Carb technical representative Guss van der Merwe tells Mining Weekly that the company has completed the CrC wear plate installation for seven chutes, the most recent one having been completed in July 2015.
He notes that, on average, a single chute at the colliery requires about 56 wear plates, each 24 mm thick, adding that the 500 mm × 500 mm wear plates are manufactured to the mine’s chute specifications, which significantly improves installation time and subsequently reduces downtime.
Van der Merwe points out that one of the most significant advantages of using the company’s CrC wear plates in coal applications is that it prevents the material from causing blockages in the chutes. “The harder our wear plates work, the smoother they get and the easier it is for the coal to flow through the chute.”
He asserts that the wear plates have improved wear resistance, owing to the company’s trademarked carbide saturation process, known as MaxCS, which has a significantly higher CrC content than the industry standard.
“This enables our wear plates to last 8 to 12 times longer than other CrC-based wear plates, such as 400 and 500 Brinell materials.”
In addition, wear resistance is also improved by the plates’ vertical dendritic crystals that perform similarly to the bristles of a toothbrush when attacked by wear.
Van der Merwe states that when using Rio-Carb’s CrC wear plates, the welding direction has no impact on the integrity of the product, owing to the vertical crystal formations.
To ensure that every installation runs as smoothly as possible, Rio-Carb uses a precision plasma cutter to cut its CrC wear plates to a client’s specification. Van der Merwe notes that each client’s specification is allocated a unique part number, which is plasma-engraved on the back of each wear plate, enabling clients to order the correctly sized wear plate without having to take any measurements.
Rio-Carb can also plasma cut countersunk insert holes into the wear plates, which enables a single operator to feed the bolt inserts through the plates and fasten them to the chute. Van der Merwe explains that the countersunk fastening configuration offers a more secure fit and simplifies liner removal when using the company’s rapid removal hardfaced countersunk bolts, known as R-R liner removal system.
Meanwhile, Van der Merwe highlights that Rio-Carb offers a free wear survey using ultrasonic measuring equipment to determine the thickness of wear liners and pipeline walls, as well as the areas where wear is most prevalent.
The survey can also predict the rate of wear, enabling plant maintenance personnel to plan shutdowns to replace wear plates.