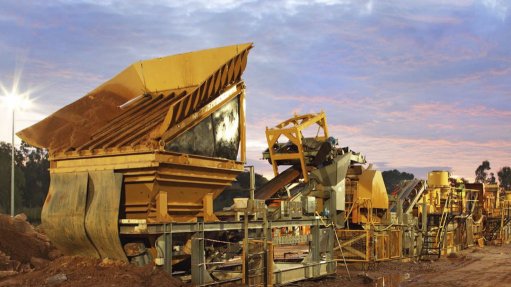
PYTHON ENVIRONOMIC PROCESSING PLANT The plant is ideal for use in remote or underground operations and was also chosen by TMAC owing to its energy efficiency, low footprint and height design
Photo by: Gekko Systems
The first two gold pours were successfully completed in February by Canada-based emerging gold producer TMAC Resources at its Doris mine and mill complex at the Hope Bay gold project, which is located in the Arctic Circle of Nunavut, in Canada.
Mineral processing equipment manufacturer Gekko Systems Africa sales and operations manager Gerhard Bezuidenhout says that the pour at the Hope Bay project may well mark the beginning of a new technological generation in mining in a “standout emerging goldfield”.
Bezuidenhout was speaking at an event hosted by the Southern African Institute of Mining and Metallurgy’s Johannesburg branch, last month, where he explained that the project was making use of the company’s C$72-million low-height, modular Python Environomic processing plant.
He stated that the Python plant processing solution was “ideal” for remote or underground use and explained that the solution was selected by TMAC for a number of reasons, including speed of design and construction through to commissioning and energy efficiency, as well as the low footprint and height design.
Bezuidenhout said that these characteristics allowed for the full modular plant to be prebuilt and tested prior to shipment in containers to site. Additionally, he noted that the small footprint and head height of the process plant allowed for significant savings in the size and cost of the process facility.
The complete modular plant was designed, fabricated, assembled and tested at Gekko’s Ballarat plant, in Victoria, Australia, after which it was packed and shipped. Bezuidenhout recounted how, in July 2016, a full shipment of 200 containers was loaded at Geelong port, in Australia, and shipped off to the project in the extremely remote region of Canada. The containers, following a three-month journey, were unloaded and ready for destuffing in September 2016.
“In only four months, the Gekko Python was unpacked and installed at TMAC’s 4 000 m2 purpose built facility,” he highlighted.
Commissioning of the plant started in January, with the first gold pour taking place on February 9. Commercial gold production is forecast for the first quarter of 2017.
The next steps for TMAC are to ensure improved process efficiencies, on-site operator training, ramp-up to steady-state production and the attainment of commercial production during this quarter.
Production of the second stage of TMAC’s Doris processing plant has started at Gekko’s Ballarat facility for the 2017 sealift.
Over the life of Hope Bay, TMAC expects to achieve a 91% recovery rate, with expected head grades of 11.4 g/t of gold. The plant has been designed for “highly efficient” gold and sulphur liberation in remote environments.
He added that the plant was designed to initially treat 1 000 t of mill feed a day by the end of the first stage of the project and would reach its maximum capacity during the second stage of 2 000 t/d by early 2018.
“The second stage of the project will include a second Python train, which comprises crushing, a gravity circuit, milling, flotation and other associated equipment,” Bezuidenhout concluded.