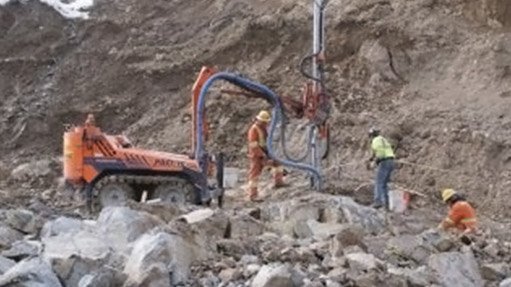
TORONTO (miningweekly.com) – Canadian miner Copper Mountain Mining on Friday reported that a transformer powering the No 2 ball mill at its eponymous mine had failed, reducing mill throughput by about 25% for about a week.
The Vancouver-based miner said spare coils were available and ABB Transformers had expedited crews to the mine to make the necessary repairs.
As part of the original design plan for the concentrator, the two ball mills and the semi-autogenous (SAG) ball mill have identical motors and transformers that are interchangeable in the event of a component failure.
The concentrator was, however, still able to continue to operate with the SAG mill and the No 1 ball mill at a reduced throughput. It was expected that output would be limited to about 1 050 tonnes per operating hour (tpoh) or about 25 000 t/d until repairs were completed.
“This transformer failure is a disappointing event for the operation at this time as our team has been making significant strides in improving tonnage through the SAG mill,” president and CEO Jim O’Rourke said.
Copper Mountain said October output was on schedule for 6.5-million pounds and, despite this event slightly impacting on metal production, all resources were being applied to minimise the impact.
The company reiterated its 2013 guidance of 65-million to 70-million pounds of copper.
Laurentian Bank Securities metals and mining analyst Christopher Chang said that during the transformer failure that occurred between May 18 and June 9, the operation processed ore at a rate of 1 207 tpoh under a similar constrained one ball mill and one SAG mill setup.
“While we believe the operation could likely produce at a similar rate, we do not believe investors will likely give the company credit for this given the operation’s challenging history,” he said in a note to clients.
He added that while the high-intensity blasting and contractor precrushing solution appeared to be an effective interim solution, he believed the operation could continue to experience occasional hiccups until the secondary crusher was permanently installed, expected at the end on 2014, which should give the operation more consistency.