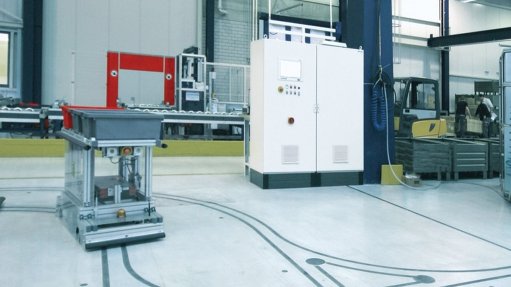
FOLLOW THE TRACK SEW-Eurodrive's automatic guided vehicle has built-in safety features that prevent accidents
South African mining companies can now benefit from drive engineering company SEW-Eurodrive’s automatic guided vehicle (AGV), which has built-in safety features that make it possible to prevent accidents, helping mineworkers to safely conduct their materials handling processes, says SEW-Eurodrive Maxolution business development and application engineer Theuns Greyvenstein.
“The AGV can be completely controlled using a programmable logic controller and requires no optical guidance for positioning. Therefore, it can go into environments that are not safe for personnel, or where high-value products are being processed, requiring limited human traffic,” he explains, adding that the AGV can have safety scanners integrated into it to help it stop automatically when people are in close proximity.
Greyvenstein tells Mining Weekly that the pricing of the AGV will be determined by the company that SEW-Eurodrive partners with to assemble the unit. “Our role is to partner with a system integrator that builds the unit. We provide the control electronics, motors, gearboxes and communication systems, while our partner will conduct the installation and building of any electrical and mechanical requirements.”
He adds that all the components used to assemble the AGV are CE-certified, while the vehicle’s safety concepts and equipment meet the requirements of the European Machine Directive and ISO 12100:1.
SEW-Eurodrive’s AGV also features wireless power transfer and communication that enable high degrees of flexibility when interfacing with the vehicle. “This enables fluid production changes, should the plant’s production line needs change, and wireless inductive power transfer, which eliminates wear and tear, as well as the corrosion of conductors. This limits downtime, lowers maintenance costs and improves the general safety of the AGV,” says Greyvenstein.
He adds that the completely wireless nature of the AGV makes maintenance easier, “as a vehicle can be quickly and easily removed from a track and be replaced by a spare unit, with minimal downtime”.
In addition to being easy to maintain, Greyvenstein says the AGV is easy to operate and exhibits great industrial robustness. Another advantage is that it would be easy to incorporate additional vehicles in the system, should more vehicles be needed as a plant grows.
The AGV is a ground-based mobile system that uses inductive power supply in the form of transfer cables that are embedded in the floor.
The vehicle uses SEW’s standard MoviTrans solution, a contactless energy transfer system, to provide contactless power transfer and SEW’s Maxolution leakage cable for wireless communication.
The AGV uses a special inductive antenna to guide the system on the track. The antenna also enables the system to take turns where the track and process layout requires it, explains Greyvenstein.
Several factors – including total cost of ownership, ease of maintenance, energy calculations, terrain, special environmental requirements and the amount of safety and human interaction required – are considered when creating a tailor-made solution for a client, he says.
“The AGV is suitable for use in a variety of industries, such as the mining, food and beverage, automotive, water treatment, timber, sugar and packaging industries.
“Calling on global expertise and local market knowledge, we offer customers optimised power, customised configuration and reliability; our drive solutions set the standard for the world of motion. This applies to drive technology, modern drive automation and, increasingly, system integration,” concludes Greyvenstein.