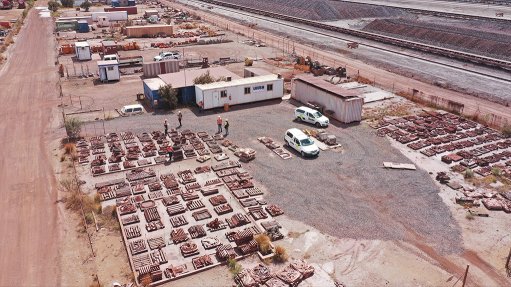
Planning, including stockholding of spare parts, can be done in advance with the reliability model in place
Transfer chute wear life measurement, an intricate process involving meticulous tracking of multiple components, is essential for enhancing uptime in materials handling applications — a direct contributor to operational efficiency. Izak Potgieter, Quality Systems Engineer at Weba Chute Systems, says that in its relentless pursuit of innovative solutions, the company pioneered a state-of-the-art reliability model which has over time gained momentum with many plants relying on this to predict maintenance requirements. The model embodies a specialised approach to the intricate task of chute wear monitoring.
"Our custom reliability model is adeptly engineered to encapsulate pivotal wear indicators for each chute,” Potgieter explains. “This level of precision enables us to accurately predict the wear life of individual components, from liners to lips and beyond."
For the model to function optimally, the integration of specific data is imperative—especially wear measurements obtained during regular inspections. Potgieter says that the discernment of wear patterns is of paramount significance, and that when furnished with this intel, plant operators are in a position to judiciously forecast which components necessitate imminent substitution.”
This capability is indispensable, and facilitates accurate and methodical planning, such as the timely procurement of pivotal components. It also strengthens preventive maintenance measures. The consequent elimination of unanticipated downtime safeguards a plant against disruptions and the ensuing loss of precious production hours.
“The capability to precisely predict component wear life has catapulted our maintenance paradigm to unparalleled heights, and this approach has received increased interest from customers, both those with Weba chute installations and other customer who are looking to changeover to more cost efficient transfer points,” he says. “While this tool is integral to our maintenance contracts, it merits mention that customers who do not have such agreements can still make use of this service from us.”
An auxiliary benefit of the reliability model is a comprehensive monthly dossier, providing stakeholders with timely alerts regarding maintenance requirements for each wear part within all chutes. The sophistication of this model is evidenced in its capacity to mirror differential wear levels across varied chute sections—especially those experiencing disparate impact levels. This granularity facilitates a targeted maintenance strategy, bolstering performance and longevity.