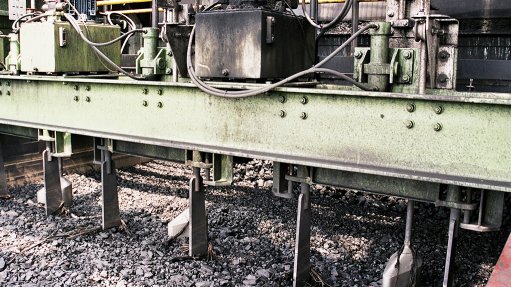
Company Announcement - MBE Minerals South Africa, with a legacy of over 40 years on the African continent, will share its technology capabilities and services with visitors to BAUMA ConExpo. Managing director, Johannes Kottman explains that the company is focused on providing a complete technical solution to the mining sector that encompasses innovative technology, capital equipment and support services.
As one of the leading suppliers of iron ore and coal beneficiation technology, MBE Minerals offers basic and detailed engineering, components for complete plants and systems including modernisation and capacity increase measures, as well as automation and process control equipment. The company’s scope of services includes feasibility studies, raw material testing, financing concepts, erection and commissioning, personnel training and pre- and aftersales services. Available technologies include its Pneuflot® flotation, BATAC® jig, ROMJIG®, Jones® Wet High Intensity Magnetic Separator (WHIMS), PERMOS® (LIMS), the Palla Vibrating Mill®, TESKA® HMS Separator and a wide variety of screens and feeders.
Kottman says that MBE Minerals’ Pneuflot® technology is attracting worldwide attention as a flotation technology of the future. “This technology has already surpassing the popularity of conventional technology as the flotation cell improves product quality and recovery and delivers lower operating cost while increasing efficiencies. MBE Minerals SA’s BATAC® jig technology has been field-proven through extensive and diverse test work to deliver higher efficiency, huge economic benefits, better product quality, better machine availability and higher throughput rates. The main advantages are its excellent separation accuracy, its relatively small footprint and comparatively low capital cost.
Since its introduction to the marketplace, the ROMJIG® has proved particularly suitable as a reliable and economical solution in destoning raw coal. The lower percentage of refuse in the washery feed means reduced wear on machinery and transporting equipment, less degradation, less dust and slurry and reduced consumption of flocculation and flotation agents in downstream fines recovery circuits. The robust Jones® Wet High Intensity Magnetic Separator, operated at up to 14 500 Gaus, offers a high throughput capability coupled with simple maintenance and lower energy consumption. The WHIMS is ideally suited to treating feebly magnetic minerals with a particle range from 20 microns up to 1.5 mm with unit throughput capacities from 500 kg/h up to 250 tph. Significantly, MBE Minerals SA recently completed the largest WHIMS plant in the world outside of Brazil in the Northern Cape.
The Permos® Medium Intensity Magnetic Separator drum type unit from MBE Minerals SA is suitable for materials which can be attracted by a field strength of between 2 000 and 5 000 Gaus. “Designs for both dry and wet feeding are available from MBE Minerals SA,” Kottman says.
The Palla Mill® offers the flexibility of being suitable for wet and dry applications in primary and secondary grinding and for pulverising materials of any hardness. It is capable of grinding more than 100 different materials, including a range of minerals and commodities previously considered unviable due to the costs involved. MBE Minerals SA also manufactures a variety of vibrating screens, available up to 3.6 m in width and 6.75 m in length, in single or double deck configuration and in either circular or linear motion. The company’s screens have been operating in the African mining industry for the past 40 years, mainly in the coal, diamond and iron ore sectors. With products for sizing, scalping, dewatering and media recovery, each screen is designed with sound mechanical features, including vibration damping, side plates, cross members and the appropriate feed and discharge chutes. All types of screening surfaces can be accommodated.
MBE Minerals SA receives expertise and technical support from its worldwide network, including the MBE Coal and Minerals Technology’s R&D centre in Cologne, Germany. The R&D centre consults with customers from all parts of the world with regard to optimum processing and this service is backed up by an in-house laboratory facility and pilot test work capabilities. The centre is also used as a training facility for customers, either on general mineral processing or on the operation and maintenance of specific MBE equipment.