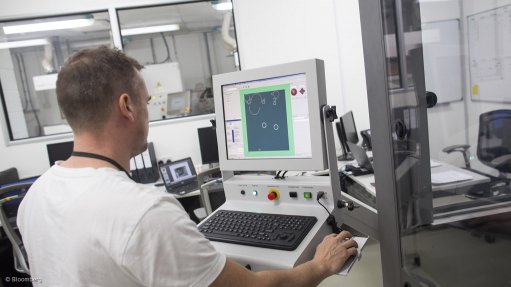
OPERATIONAL CONTROL
By 3D printing the spare parts and replaceable components that complex mine machinery requires, operators can gain greater control over the supply chain
Photo by: Bloomberg
Forward-thinking mining organisations are realising that industrial-scale, three-dimensional (3D) printing of equipment used in mines could make operations more cost effective and reduce the frustrations of equipment downtime, says information technology consultancy and systems integration firm Wipro South Africa energy and natural resources director Louise Steenekamp.
“By 3D-printing the spare parts and replaceable components that complex mine machinery requires, operators can gain greater control over the supply chain and ensure the smooth running of equipment.”
She avers that the current methods of producing tooling and components are often time-consuming, expensive, wasteful and rely too much on third-party equipment manufacturers. “[Further], mines have to bear the brunt of excess inventory, warehousing and storage costs, as well as the logistical costs of urgently transporting parts.”
Steenekamp believes that 3D printing is at the nexus of information technology and operational technology and that, as these realms are moving closer to each other, interesting opportunities for miners will emerge.
Miners worldwide must dig at greater depths to find seams of resources and, therefore, use mining equipment that needs to be monitored and maintained, she says.
“By using robotics and other machines fitted with sensors, we can create a digital representation – such as a hologram or on-screen display – of the equipment to [monitor and] understand its performance, and interaction with the environment kilometres below the surface,” Steenkamp explains.
Subsequently, by leveraging this sensory data, companies can start to predict when equipment may fail, need servicing or require new parts.
“The data can be fed into the 3D printing systems to ensure that the required components are produced on the surface and sent down, ready for when they’re needed,” Steenekamp advances.
Different mining environments require different approaches and tools, which subsequently makes the cost-effective production of unique and customised items, even in small quantities, the most significant advantage of 3D printing, compared with traditional mass-scale manufacturing.
“For mine operators looking to tailor their approach to a specific site, 3D printing offers some exciting prospects . . . it could not only save costs and reduce the interruptions and waiting times for maintenance but also be the catalyst for smarter operations throughout a mine’s operations,” Steenekamp remarks.
She believes that managers gain “unprecedented vision into the future”, while also having the ability to build customised components before they are needed and dynamically adjusting operations.
Further, additional operations, such as labour-shift scheduling and truck dispatch timetables, can be configured to best fit with the ebbs and flows of mine operations.
“In the digital era, South African miners, similar to their international peers, are looking to technology-led efficiency gains as the primary driver of growth over the coming years. And advancements in 3D printing could be a vital enabler,” Steenekamp concludes.